Gyenge László régóta foglalkozik fenntarthatósági lehetőségekkel és körforgásos gazdasági modellekkel, ám a design karóra iparnál azt vette észre, hogy nem helyeznek nagy hangsúlyt az igazi megoldásokra.
Így azt vette a fejébe, hogy ő fog ezzel foglalkozni, barátjával, Petrosszal együtt, aki építész, tervező, és benne van mindenben, ami a kreatív energiákat mozgatja meg benne.
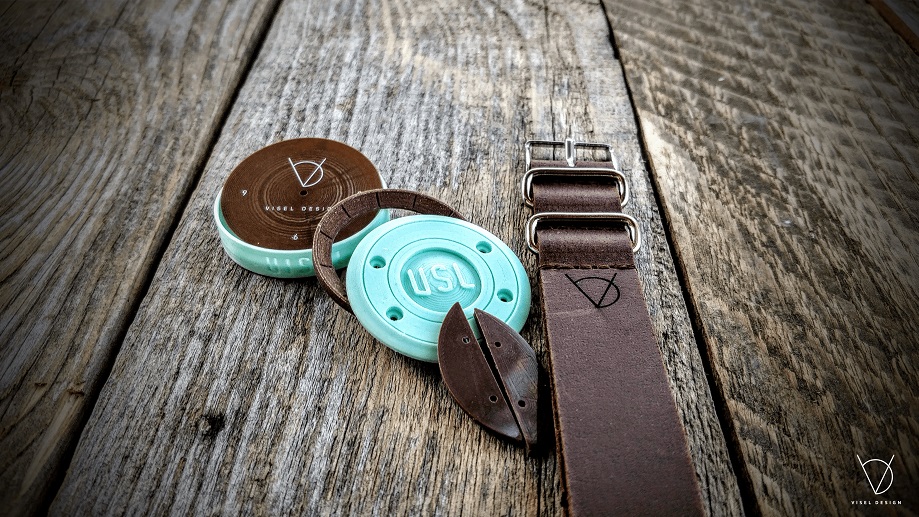
Miért pont a 3D nyomtatás lett a megoldás?
Az elején még a fa karórákat és a CNC-marás technikát gondoltuk jó megoldásnak. Elkészült az első modell, de folyamatosan falakba ütköztünk a gyártás során. Elmentünk tíz szakemberhez, de senki nem akarta még a prototípust sem legyártani.
Eközben azért már nézegettük a 3D nyomtatós videókat, blogokat, kezdtünk ismerkedni a technikával és az anyagokkal.
A 3D technológia is fenntartható gyártási forma, ahol rétegek lerakásával készül el a tárgy, szemben a hagyományos megmunkálással, ahol leválasztjuk a felesleges anyagot, amivel rengeteg hulladékot termelünk.
Modellünk már volt, így elvittük egy csapathoz, akik saját fejlesztésű 3D nyomtatókat gyártottak. Egy hét múlva, 2016-ban elkészült az első 3D nyomtatott karóratokunk, 2018-ra pedig megszületett az első olyan prototípus, amely már hordható volt, és a saját nyomtatónkkal gyártottuk.
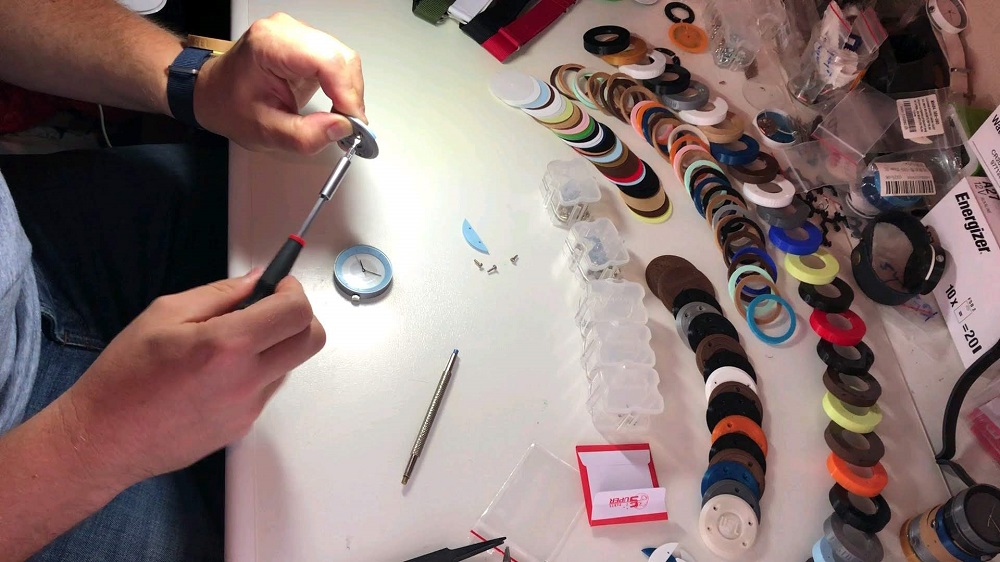
Készítettünk is a barátoknak, ismerősöknek, akiktől számtalan hasznos, használható és pozitív visszajelzést kaptunk. Ezekből rengeteget tanultunk, és sokat fel is használtunk közülük.
Környezettudatos alapanyagok
Az óráink öt részből állnak: tok, hátlap, perem, skála, számlap, ezeket nyomtatjuk ki 3D technikával. Az alapanyag a PLA (politejsav), azaz bioműanyag, ami legtöbbször kukoricakeményítőből készül.
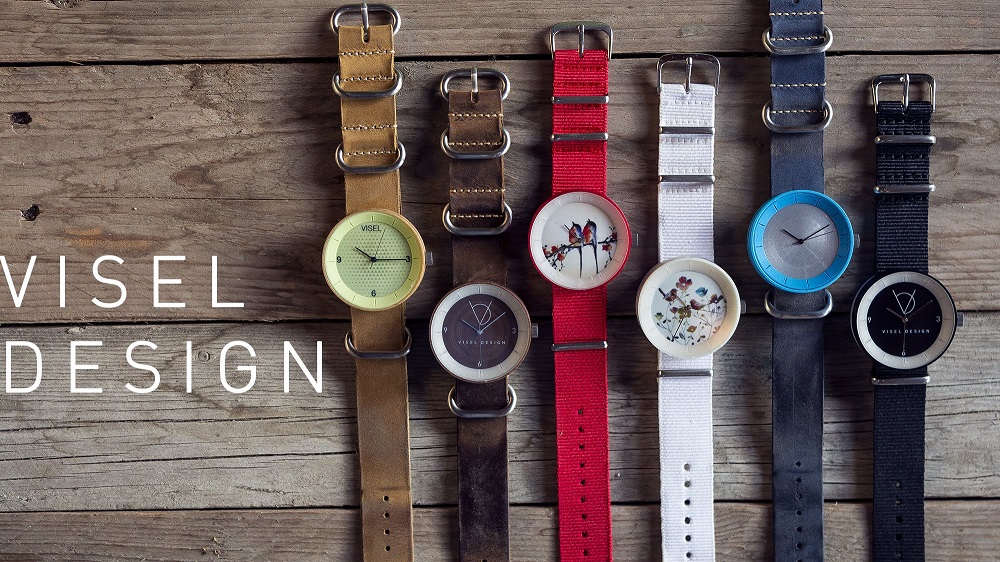
Van másik kedvenc alapanyagunk is, amivel egy kicsit visszanyúlunk a kezdetekhez (fa karóra). Ez egy speciális bioműanyag és fapor keveréke, amelynek a nyomtatás után igazi fa hatása van, sőt nyomtatás közben még faillata is!
Fontos megjegyezni, hogy ez az alapanyag egyelőre csak speciális körülmények között komposztálható. Az órák számlapjai UV nyomtatással készülnek, ezzel a technológiával nincsenek határok, ha szép, egyedi és izgalmas design órákat szeretnénk gyártani!
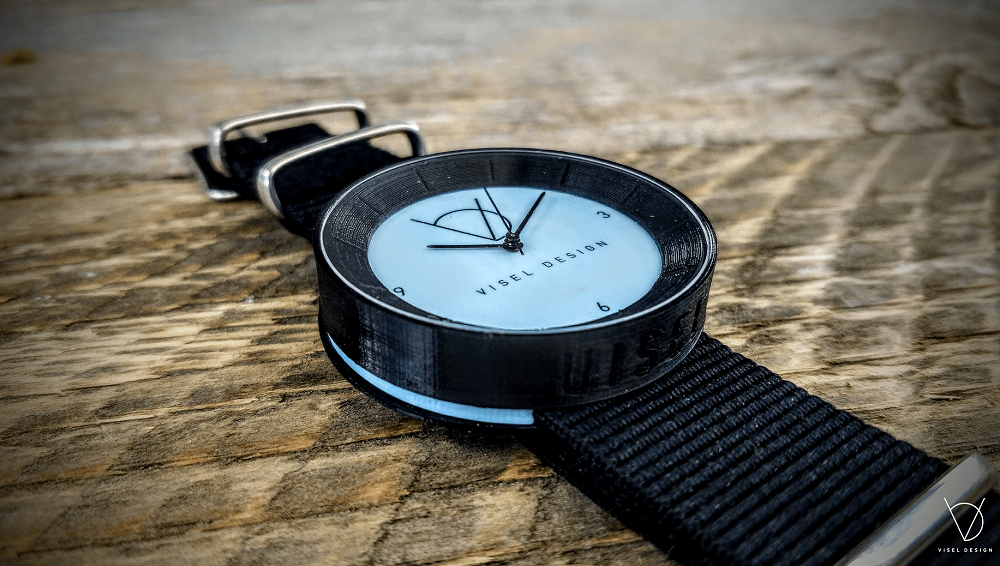
Lehet teljesen egyedi az órád!
Ha valaki egyedi Visel Design karórát szeretne, a weboldalunkon lévő karóratervezővel meg tudja tervezni a saját elképzelése szerint, a tok/hátlap, a számlap, a skála, a perem színe változtatható. A használata pofonegyszerű, mert csak rákattintasz az alkatrészre és a színskálából kiválasztod a színt, és már látod is az eredményt.
55 perc alatt készül el egy karóra!
Ha minden alkatrészt egyszerre szeretnénk kinyomtatni, akkor 3 óra a nyomtatási idő. Ez nem túl jó hír, ha azt nézem, hogy egy nyolcórás munkaidőben csak 2 órát tudunk elkészíteni.
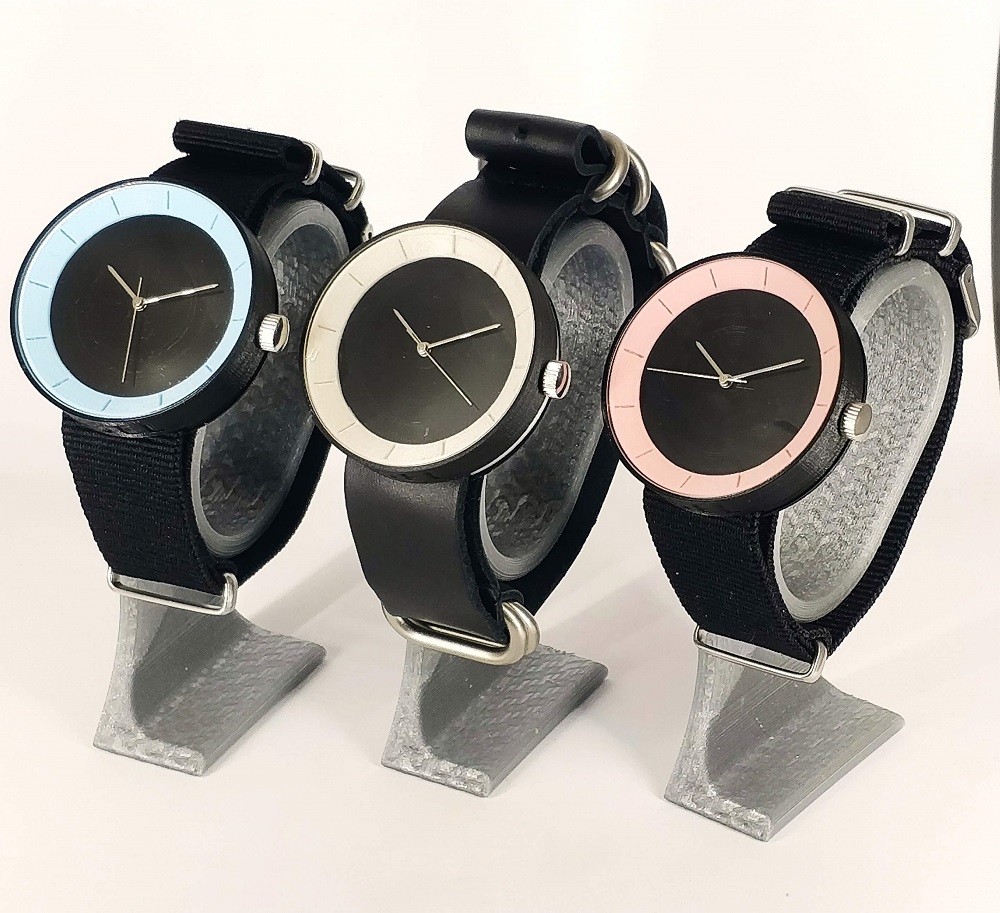
Egy képzés alkalmával találkoztam a LEAN-menedzsmenttel, ami nagyon sokat segített, hogy ezen javítsunk. Ezt úgy értük el, hogy a két nagy alkatrészből (tok, hátlap) tartunk minikészletet, minden színből 2 darabot. A számlapok előre ki vannak nyomtatva, mert azokra UV nyomtatással kerül fel a design.
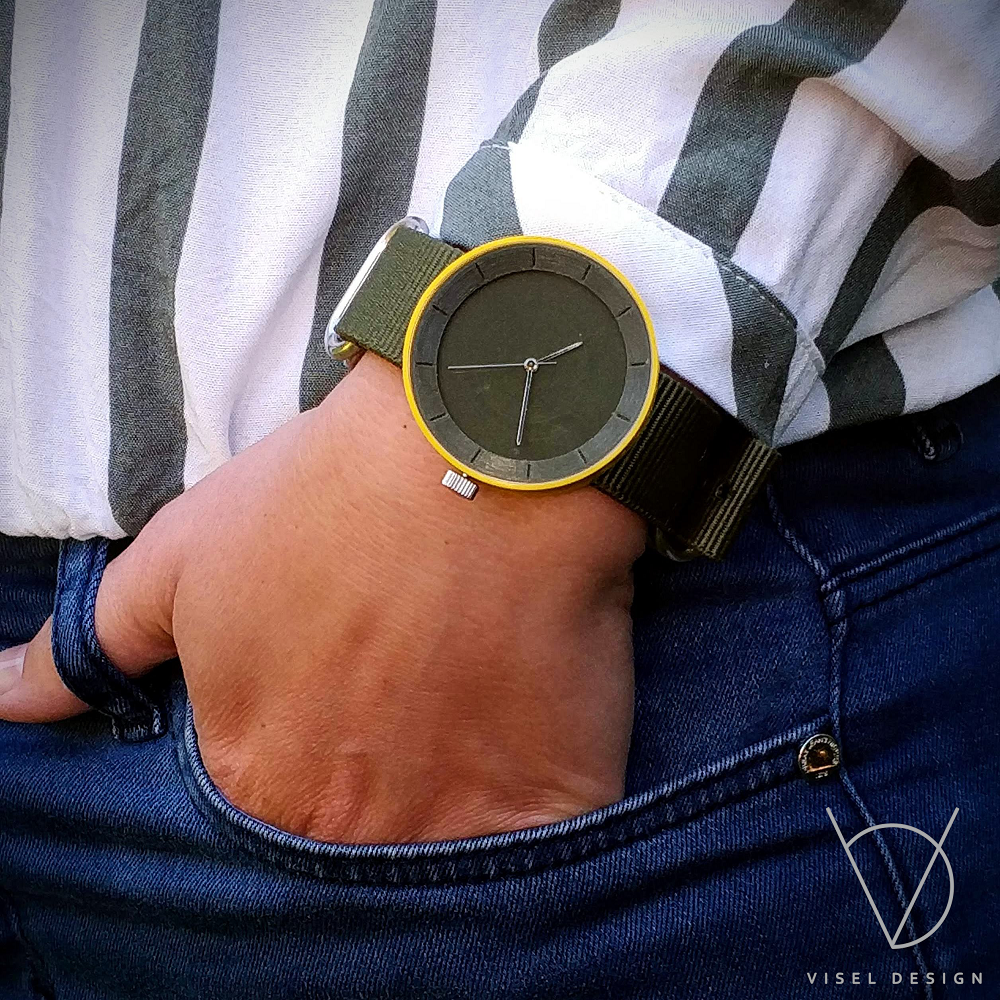
Így a perem és a skála nyomtatása közben (kb. 30 perc) belerakom a tokba az óraművet, beragasztom a számlapot és felteszem a mutatókat. A skálát a helyére illesztem, és az beragasztom óraüveget. A végén 4 csavarral a hátlapot és a peremet rögzítem a tokhoz. Átfűzöm a szíjat, és a 3D nyomtatott dobozba teszem az elkészült karórát. 55 perc a 3 óra helyett! Na ez így már jobban hangzik!
További tartamat az alábbi linkeken találsz
/alkotoenergia
Visel Design
/alkotoenergia
Visel Design